2024 लेखक: Howard Calhoun | [email protected]. अंतिम बार संशोधित: 2023-12-17 10:28
आज, बड़ी संख्या में विभिन्न चीजें, पुर्जे आदि स्टील से बने होते हैं। स्वाभाविक रूप से, इसके लिए बड़ी मात्रा में स्रोत सामग्री की आवश्यकता होती है। इसलिए, संयंत्र लंबे समय से स्टील की निरंतर ढलाई की विधि का उपयोग कर रहे हैं, जिसकी विशेषता सबसे महत्वपूर्ण विशेषता - उच्च उत्पादकता है।
कार्य के लिए आवश्यक उपकरण
आज तक, इस तरह से स्टील की ढलाई के लिए कई प्रतिष्ठानों को जाना जाता है, और उन्हें यूएनआरएस के रूप में संक्षिप्त किया जाता है। प्रारंभ में, एक ऊर्ध्वाधर-प्रकार की स्थापना विकसित की गई थी और कार्यशाला के तल के स्तर से 20-30 मीटर नीचे स्थित उत्पादन में डाल दी गई थी। हालांकि, बाद में फर्श की गहराई को छोड़ने की इच्छा इन प्रतिष्ठानों के विकास के लिए मुख्य इंजन बन गई। इससे टावर-प्रकार के निरंतर कास्टिंग संयंत्रों का विकास और कार्यान्वयन हुआ। इन प्रतिष्ठानों की ऊंचाई 40 मीटर थी हालांकि, मशीन के इस संस्करण का व्यापक रूप से दो कारणों से उपयोग नहीं किया गया था। सबसे पहले, निर्माणकार्यशाला में ऐसी इकाई काफी समस्याग्रस्त और श्रमसाध्य है। दूसरे, इसके संचालन से और भी कठिनाइयाँ उत्पन्न हुईं।
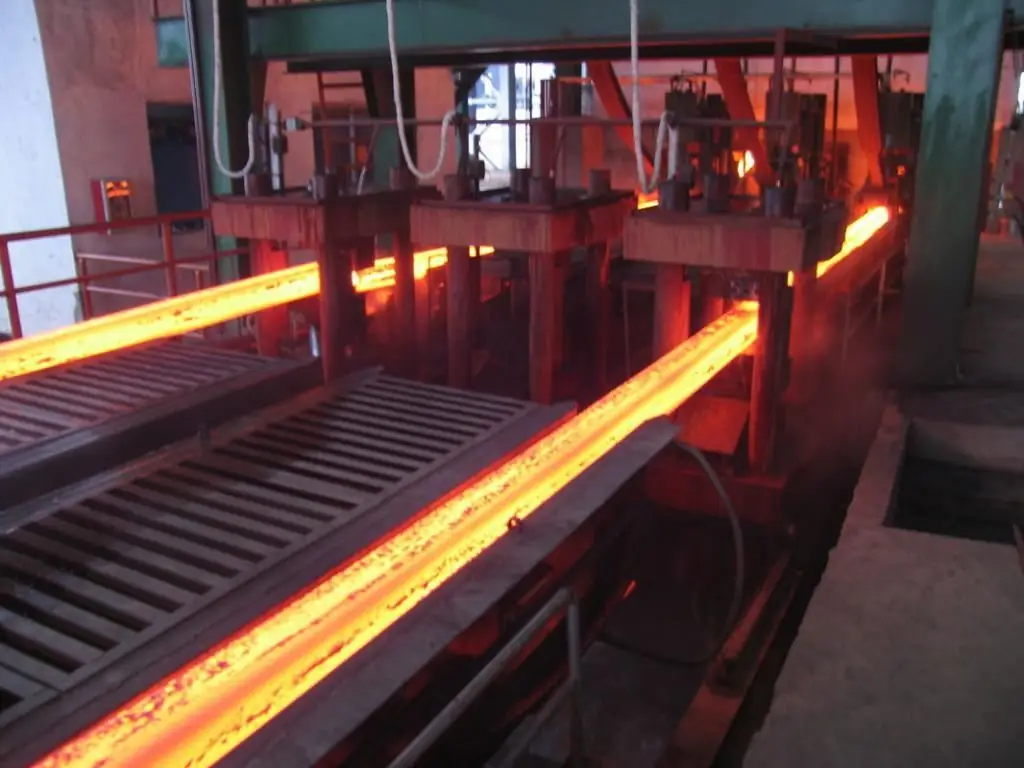
घुमावदार और रेडियल इंस्टॉलेशन
समय के साथ, स्टील की निरंतर ढलाई को ऊर्ध्वाधर झुकने वाली मशीनों के साथ काम करने के लिए स्थानांतरित किया गया। मुख्य विशेषता शाफ्ट के बाद 90 डिग्री से बाहर आने वाली पिंड का झुकना है। उसके बाद, पिंड को सीधा करने के लिए इंस्टॉलेशन में एक विशेष स्ट्रेटनिंग मैकेनिज्म का उपयोग किया गया था, और इस चरण के बाद ही कटिंग हुई। ऐसे उपकरणों पर लगातार स्टील की ढलाई किसी कारण से बहुत लोकप्रिय नहीं हुई है। सबसे पहले, मोड़ ने, निश्चित रूप से, ऊंचाई को कम करना संभव बना दिया, लेकिन साथ ही साथ पिंड के क्रॉस सेक्शन को गंभीर रूप से सीमित कर दिया। सामग्री के एक हिस्से को प्राप्त करने के लिए जितना अधिक आवश्यक था, उतना ही अधिक मोड़ होना चाहिए, जिसका अर्थ है कि ऊंचाई फिर से बढ़ गई। दूसरे, झुकने वाली मशीनों को स्टील की दुकानों में खड़ी मशीनों की तुलना में अधिक कठिनाइयों के साथ रखा गया था।
आज, रेडियल स्टील की निरंतर ढलाई के प्रतिष्ठान अधिक से अधिक लोकप्रियता प्राप्त कर रहे हैं। ऐसी इकाई पर, सिल्लियां सांचे में बनती हैं और उसे उसी चाप के साथ छोड़ती हैं जिससे वह उसमें प्रवेश करती है। उसके बाद, इसे एक पुल-सही तंत्र द्वारा सीधा किया जाएगा। और फिर आप पहले से ही पिंड को रिक्त स्थान में काटना शुरू कर सकते हैं। यह वह डिज़ाइन है जो व्यवहार में स्टील की दुकान में माल के प्रवाह को व्यवस्थित करने में सबसे तर्कसंगत निकला।
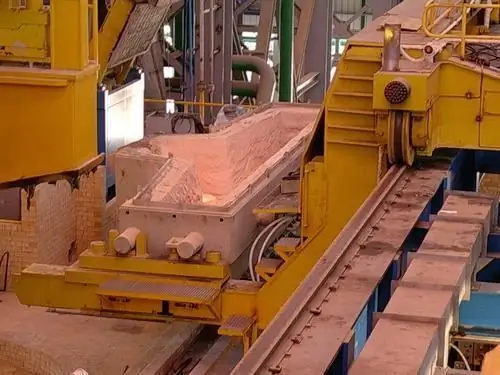
कास्टिंग कहां से शुरू होती है
निरंतर की तकनीकस्टील कास्टिंग एक जटिल प्रक्रिया है। हालांकि, यह कहना उचित है कि इस्तेमाल किए गए उत्पादन सेटअप की परवाह किए बिना सिद्धांत समान रहता है। आप एक लंबवत यूएनआरएस के उदाहरण का उपयोग करके तकनीक पर विचार कर सकते हैं।
मशीन में एक विशेष क्रेन के माध्यम से स्टील डालने के लिए एक करछुल की आपूर्ति की जाती है। उसके बाद, स्टील टुंडिश में प्रवाहित होता है, जिसमें एक स्टॉपर होता है। सिंगल स्ट्रैंड मशीनों के लिए एक स्टॉपर होगा, मल्टी स्ट्रैंड मशीनों के लिए प्रति स्ट्रीम एक स्टॉपर होगा। इसके अलावा, टुंडिश के पास लावा रखने के लिए एक विशेष बाधक है। टुंडिश से, स्टील एक डोजिंग ग्लास या स्टॉपर से गुजरते हुए, मोल्ड में प्रवाहित होगा। यहां यह ध्यान रखना महत्वपूर्ण है कि पहली ढलाई से पहले, बीज को नीचे की ओर से सांचे में डाला जाता है। यह या तो पूरे सांचे के क्रॉस सेक्शन को भरता है, या केवल वर्कपीस के आकार को। बीज की सबसे ऊपरी परत सांचे के नीचे होगी। इसके अलावा, इसमें एक पिंड के साथ भविष्य में अड़चन के लिए निगलने वाली पूंछ का आकार भी होता है।
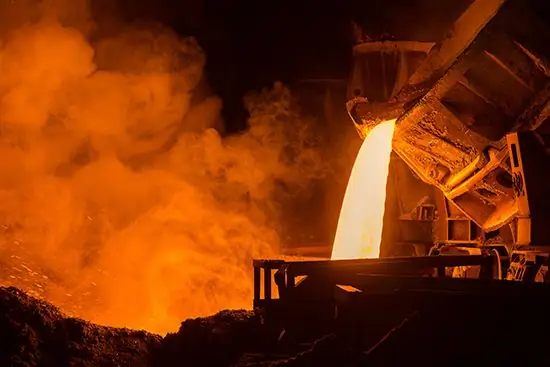
आगे की कास्टिंग
अगला, स्टील की निरंतर ढलाई की प्रक्रिया में, कच्चे माल का स्तर बीज से लगभग 300-400 मिमी की ऊंचाई तक बढ़ने तक प्रतीक्षा करना आवश्यक है। जब ऐसा होता है, तो तंत्र शुरू हो जाता है, जो खींचने वाले उपकरण को संचालन में लाता है। इसमें पुल रोल होते हैं, जिसके प्रभाव में बीज गिरेगा और निर्मित पिंड को अपने साथ खींच लेगा।
एक सतत ढलाई मशीन में आमतौर पर खोखली दीवारों के साथ तांबे का बना एक साँचा होता है। वह तीव्र के अधीन हैठंडे पानी की क्रिया से, और इसका आंतरिक भाग प्राप्त होने वाले पिंड के आकार से मेल खाता है। यहीं पर पिंड-रिक्त क्रस्ट का निर्माण होता है। उच्च ढलाई गति पर, इस क्रस्ट का फटना और धातु का रिसाव हो सकता है। इससे बचने के लिए, मोल्ड को पारस्परिक गतियों की विशेषता है।
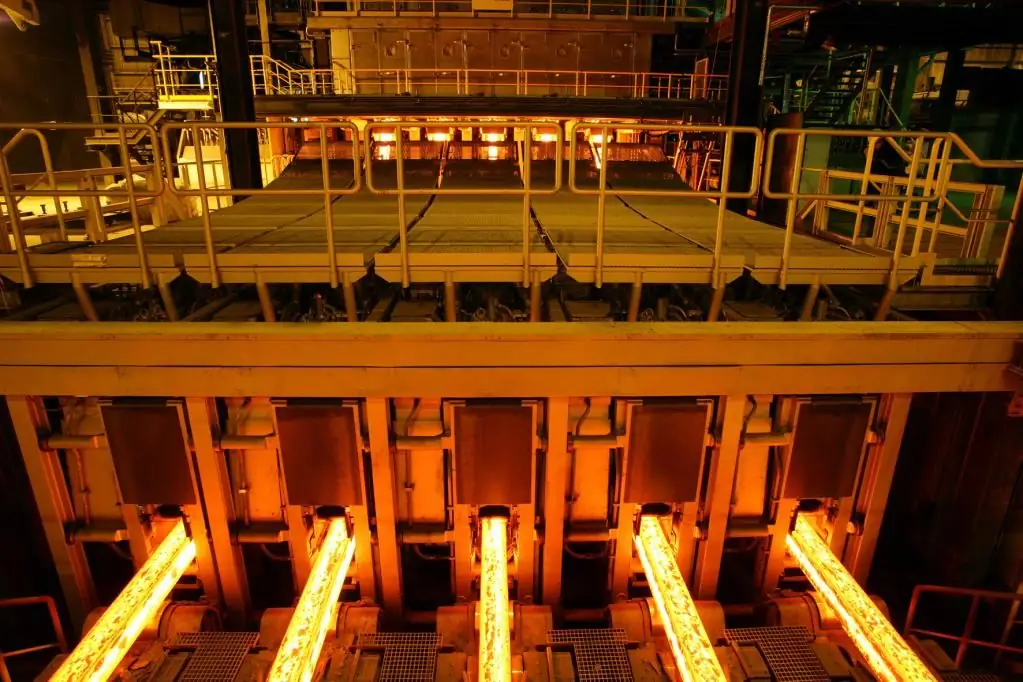
मोल्ड ऑपरेशन की विशेषताएं
निरंतर कास्टिंग मशीन में एक विद्युत मोटर होती है जो इस पारस्परिक गति को बनाने के लिए जिम्मेदार होती है। यह कैम-टाइप स्विंग मैकेनिज्म के साथ गियरबॉक्स के बल के माध्यम से किया जाता है। सबसे पहले, मोल्ड उसी दिशा में चलता है जैसे वर्कपीस, यानी नीचे, और प्रक्रिया पूरी होने के बाद, यह वापस ऊपर आ जाता है। स्विंग स्ट्रोक 10 से 40 मिमी तक होता है। मोल्ड किसी भी प्रकार के उपकरण पर स्टील की निरंतर ढलाई में एक महत्वपूर्ण कम्पार्टमेंट है, और इसलिए इसकी दीवारों को पैराफिन या विशेषताओं के लिए उपयुक्त किसी अन्य स्नेहक के साथ चिकनाई की जाती है।
यह ध्यान देने योग्य है कि आधुनिक उपकरणों में लैडल स्टॉपर पर नियंत्रण संकेत लगाकर धातु के स्तर को रेडियोमेट्रिक रूप से नियंत्रित किया जाता है। मोल्ड में ही, उत्पादन के दौरान उत्पाद ऑक्सीकरण से बचने के लिए धातु स्तर से ऊपर या तो एक तटस्थ या कम करने वाला वातावरण बनाया जा सकता है।
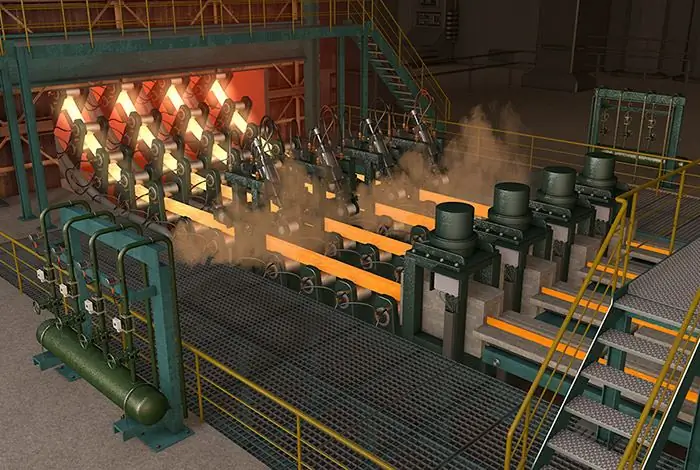
पिंड का छिलका
यह ध्यान देने योग्य है कि वैक्यूम के तहत काम करना भी एक आशाजनक कास्टिंग विधि माना जाता है। एक इकाई कर सकती हैएक साथ कई सांचों में डालना। इस प्रकार, एक संस्थापन की धाराओं की संख्या आठ तक पहुँच सकती है।
ठंडे बीज की हीट सिंक क्रिया का उपयोग पिंड की त्वचा के तल को बनाने के लिए किया जाता है। बीज के प्रभाव में पिंड मोल्ड से बाहर निकल जाएगा, जिसे सेकेंडरी कूलिंग ज़ोन (SCZ) में खींचा जाता है। बिलेट के बीच में, स्टील अभी भी तरल अवस्था में रहेगा। यहां यह ध्यान रखना महत्वपूर्ण है कि, स्टील कास्टिंग तकनीक की आवश्यकताओं के अनुसार, मोल्ड से बाहर निकलने के समय त्वचा की मोटाई कम से कम 25 मिमी होनी चाहिए। इन आवश्यकताओं को पूरा करने के लिए, सही सामग्री प्रवाह दर चुनना आवश्यक है।
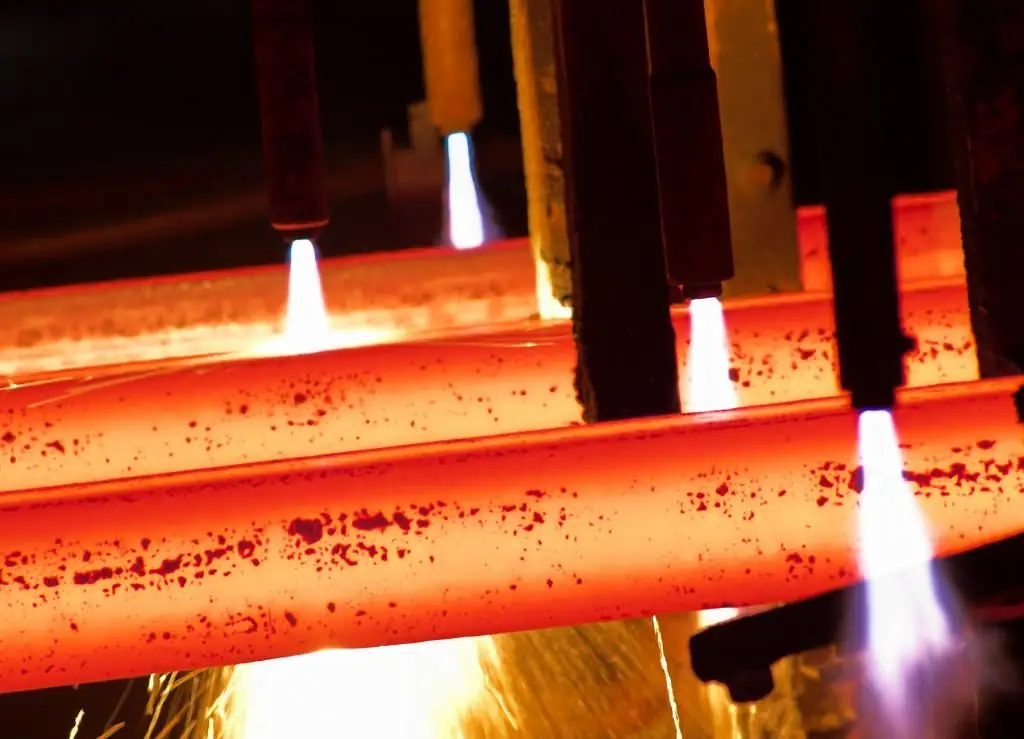
स्थापना और कास्टिंग प्रक्रिया की विशेषताएं
तकनीकी विशेषताएँ लगभग इस प्रकार हैं। यदि पिंड का खंड 160x900 मिमी है, तो इसकी गति 0.6 से 0.9 मीटर/मिनट तक होनी चाहिए। यदि क्रॉस सेक्शन 180x1000 मिमी है, तो गति 0.55-0.85 मीटर/मिनट तक कम हो जाती है। 200x200 मिमी - 0.8-1.2 मीटर/मिनट वर्ग-प्रकार के पिंड के क्रॉस सेक्शन के लिए उच्चतम गति संकेतक की आवश्यकता होती है।
उपरोक्त संकेतकों के आधार पर, हम यह निष्कर्ष निकाल सकते हैं कि निरंतर कास्टिंग तकनीक का उपयोग करते हुए एक स्ट्रैंड की औसत कास्टिंग गति 44.2 टन / घंटा है। यदि आप गति की इष्टतम दर से अधिक हो जाते हैं, तो केंद्रीय सरंध्रता बढ़ जाएगी।
इसके अलावा, यह ध्यान देने योग्य है कि कास्टिंग की स्थिरता और उत्पाद की गुणवत्ता धातु के तापमान से ही प्रभावित होती है। अनुभवजन्य रूप से, यह पाया गया कि 1560 डिग्री. से अधिक के तापमान परसेल्सियस पिंड की सतह अक्सर दरारों से ढकी होती है। यदि तापमान संकेत से कम है, तो कांच अक्सर कड़ा हो जाएगा। इस प्रकार, यह पाया गया कि स्टील की निरंतर ढलाई की विधि के लिए इष्टतम तापमान 1540-1560 डिग्री सेल्सियस होगा। इस सूचक को बनाए रखने के लिए, रिलीज से पहले भट्ठी का ताप तापमान 1630-1650 डिग्री की सीमा में होना चाहिए।
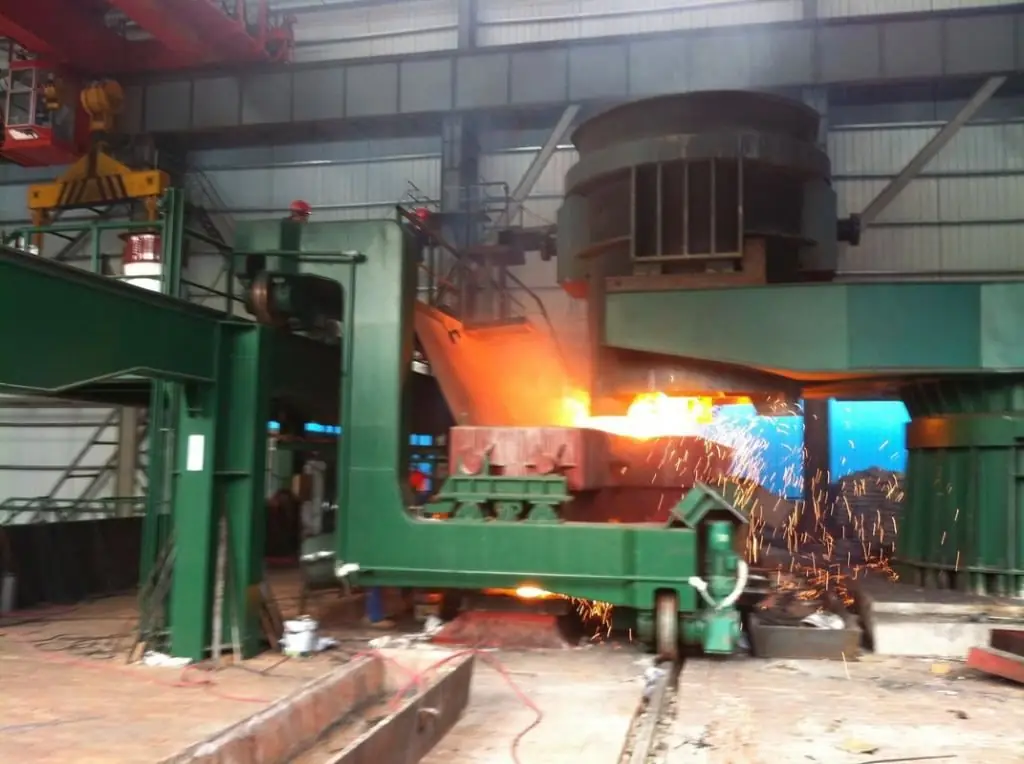
सेकेंडरी कूलिंग जोन
इस खंड में, स्प्रे से आने वाले पानी की मदद से पिंड की सबसे गहन और सीधी शीतलन की जाती है। निष्क्रिय की एक विशेष प्रणाली है, न कि पावर रोलर्स। उनका घूर्णन पिंड को झुकने या विकृत होने से रोकता है। इस क्षेत्र में तीव्र शीतलन के कारण, पिंड की दीवारें जल्दी से मोटाई में बढ़ जाएंगी, और क्रिस्टलीकरण गहराई में फैल जाएगा। पिंड खींचने की गति और उसके ठंडा होने की डिग्री इस तरह से चुनी जानी चाहिए कि जब तक पिंड पुल रोल में प्रवेश करता है तब तक वह पूरी तरह से ठोस हो जाता है।
लगातार कास्टिंग करने के क्या फायदे हैं
चूंकि स्टील की ढलाई की इस पद्धति ने सांचों में डालने की विधि को बदल दिया है, यह इस विधि से तुलना करने योग्य है। सामान्य तौर पर, यह निम्नलिखित लाभों को उजागर करने योग्य है: अधिक उत्पादकता, कम लागत और प्रक्रिया की कम श्रम तीव्रता। पिंड के निरंतर गठन के कारण, संकोचन गुहा को पिंड के सांचों के विपरीत पूंछ में स्थानांतरित किया जाता है, जहां प्रत्येक पिंड की अपनी गुहा होती है। इससे उपयुक्त धातु की उपज का प्रतिशत काफी बढ़ जाता है। UNRS आपको प्राप्त करने की अनुमति देता हैविभिन्न आकृतियों का एक वर्कपीस, एक छोटे वर्ग 40x40 मिमी से एक आयत 250x1000 मिमी तक। निरंतर कास्टिंग मशीनों के उपयोग ने स्वैगिंग मिलों को पूरी तरह से छोड़ना संभव बना दिया। इसने उत्पादन प्रक्रिया की लागत को काफी कम कर दिया, और इसलिए बाजार पर कीमत। इसके अलावा, धातुकर्म प्रसंस्करण की प्रक्रिया को सरल बनाया गया है।
खामियां
प्रक्रिया के उच्च मशीनीकरण और स्वचालन की संभावना के बावजूद, ऊपर वर्णित अच्छे सिल्लियों का एक उच्च प्रतिशत और अन्य लाभ, इस पद्धति के कुछ नकारात्मक पक्ष भी हैं। निरंतर कास्टिंग स्टील के नुकसान इस प्रकार हैं।
सबसे पहले, जटिल विन्यास के सिल्लियां उत्पन्न करने की कोई संभावना नहीं है। दूसरे, सिल्लियों और रिक्त स्थान की सीमा काफी सीमित है। एक अलग ब्रांड के कच्चे माल को डालने के लिए मशीनों को परिवर्तित करना काफी मुश्किल है, जो एक ही संयंत्र में उत्पादित होने पर एक अलग ब्रांड के उत्पाद की अंतिम लागत को बढ़ा सकता है। कुछ स्टील ग्रेड, उदाहरण के लिए, उबलने वाले, इस विधि का उपयोग करके बिल्कुल भी नहीं बनाए जा सकते हैं।
स्टील की ढलाई की निरंतर विधि का अंतिम नुकसान बहुत महत्वपूर्ण है। यह एक संभावित उपकरण विफलता है। यूएनआरएस की विफलता से प्रदर्शन में भारी नुकसान होगा। मरम्मत में जितना अधिक समय लगेगा, नुकसान उतना ही अधिक होगा।
सिफारिश की:
खाद्य स्टेनलेस स्टील: गोस्ट। खाद्य ग्रेड स्टेनलेस स्टील की पहचान कैसे करें? खाद्य स्टेनलेस स्टील और तकनीकी स्टेनलेस स्टील में क्या अंतर है?

लेख खाद्य ग्रेड स्टेनलेस स्टील के ग्रेड के बारे में बात करता है। खाद्य स्टेनलेस स्टील को तकनीकी से अलग करने का तरीका पढ़ें
डायमंड बोरिंग मशीन: प्रकार, उपकरण, संचालन सिद्धांत और संचालन की स्थिति
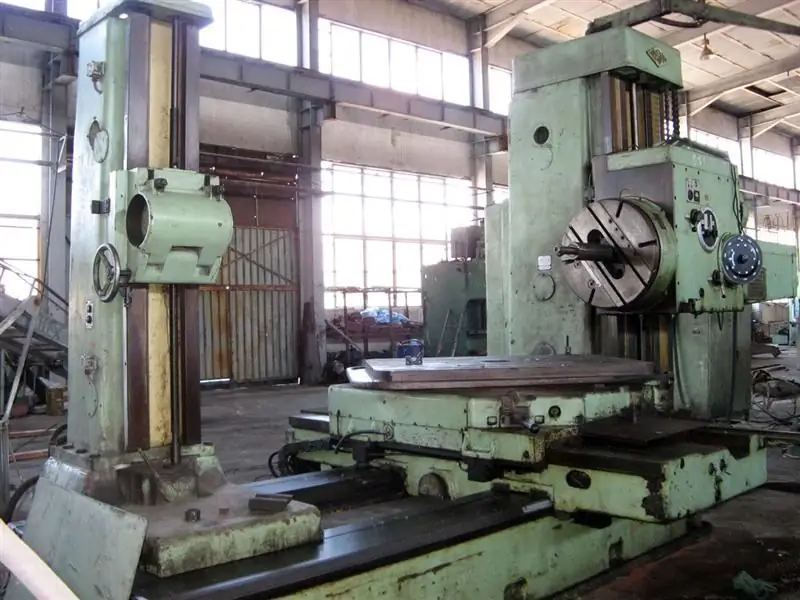
एक जटिल कटिंग डायरेक्शन कॉन्फ़िगरेशन और सॉलिड-स्टेट वर्किंग इक्विपमेंट का संयोजन डायमंड बोरिंग उपकरण को अत्यंत नाजुक और महत्वपूर्ण धातु संचालन करने की अनुमति देता है। ऐसी इकाइयों को आकार की सतह बनाने, छेद सुधार, सिरों की ड्रेसिंग आदि के संचालन पर भरोसा किया जाता है। साथ ही, डायमंड बोरिंग मशीन विभिन्न क्षेत्रों में आवेदन संभावनाओं के मामले में सार्वभौमिक है। इसका उपयोग न केवल विशिष्ट उद्योगों में, बल्कि निजी कार्यशालाओं में भी किया जाता है।
लेटरप्रेस है लेटरप्रेस प्रिंटिंग तकनीक, विकास के आधुनिक चरण, आवश्यक उपकरण, इस प्रकार की छपाई के फायदे और नुकसान
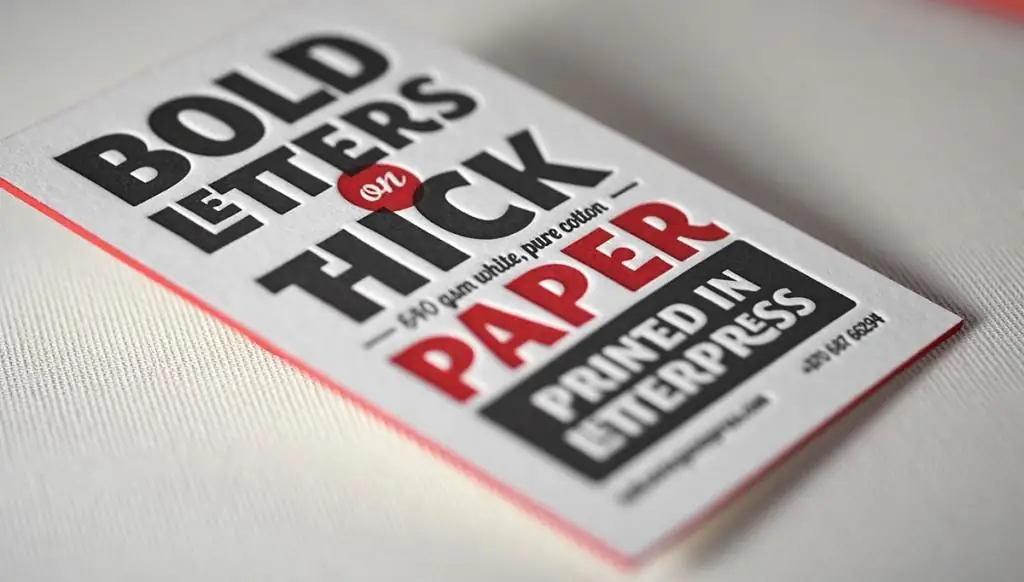
लेटरप्रेस रिलीफ मैट्रिक्स का उपयोग करके जानकारी को लागू करने के विशिष्ट तरीकों में से एक है। जो तत्व बाहर निकलते हैं उन्हें एक पेस्ट के रूप में पेंट से ढक दिया जाता है, और फिर कागज के खिलाफ दबाया जाता है। इस प्रकार, विभिन्न जन पत्रिकाओं, संदर्भ पुस्तकों, पुस्तकों और समाचार पत्रों को दोहराया जाता है।
डीजल संचालन सिद्धांत: विशेषताएं, फायदे और नुकसान
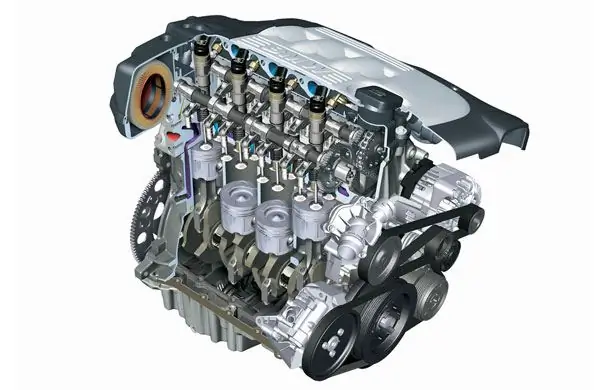
हमारी सड़कों पर डीजल कारें किसी भी तरह से असामान्य नहीं हैं। पश्चिमी यूरोप के देशों में, वे बहुमत में हैं। गैसोलीन इंजन पर डीजल इंजन के कई फायदे हैं। लेकिन साथ ही, कुछ कमियां भी हैं। यह मोटर क्या है, डीजल उपकरण क्या है और संचालन का सिद्धांत क्या है? हमारे आज के लेख में विचार करें
डीजल पनडुब्बी: निर्माण का इतिहास, नाव परियोजनाएं, संचालन का सिद्धांत, फायदे, नुकसान और विकास के चरण
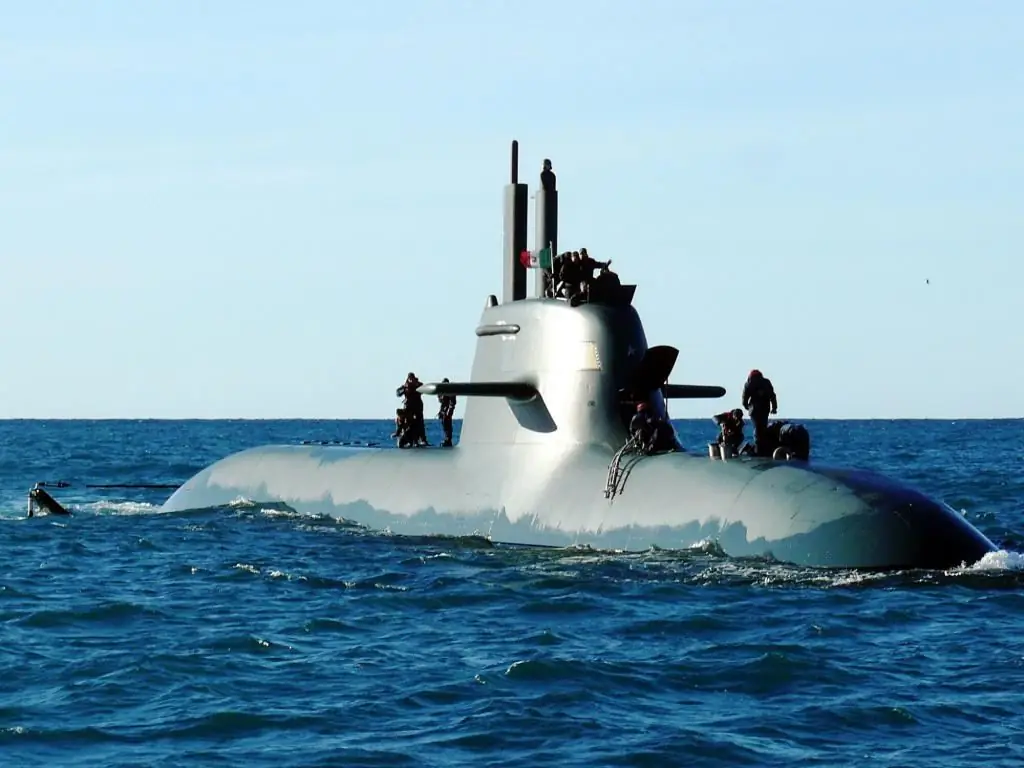
पानी के नीचे एक पनडुब्बी बनाने का विचार, वास्तव में एक पनडुब्बी का एक प्रोटोटाइप (बाद में एक पनडुब्बी के रूप में संदर्भित), 18 वीं शताब्दी में उनकी वास्तविक उपस्थिति से बहुत पहले पैदा हुआ था। कई किंवदंतियों में पानी के नीचे के वाहनों का कोई सटीक विवरण नहीं है, न ही पुनर्जागरण प्रतिभा लियोनार्डो दा विंची में।